Understanding Manifold Valve Function: A Key Component in Fluid Systems
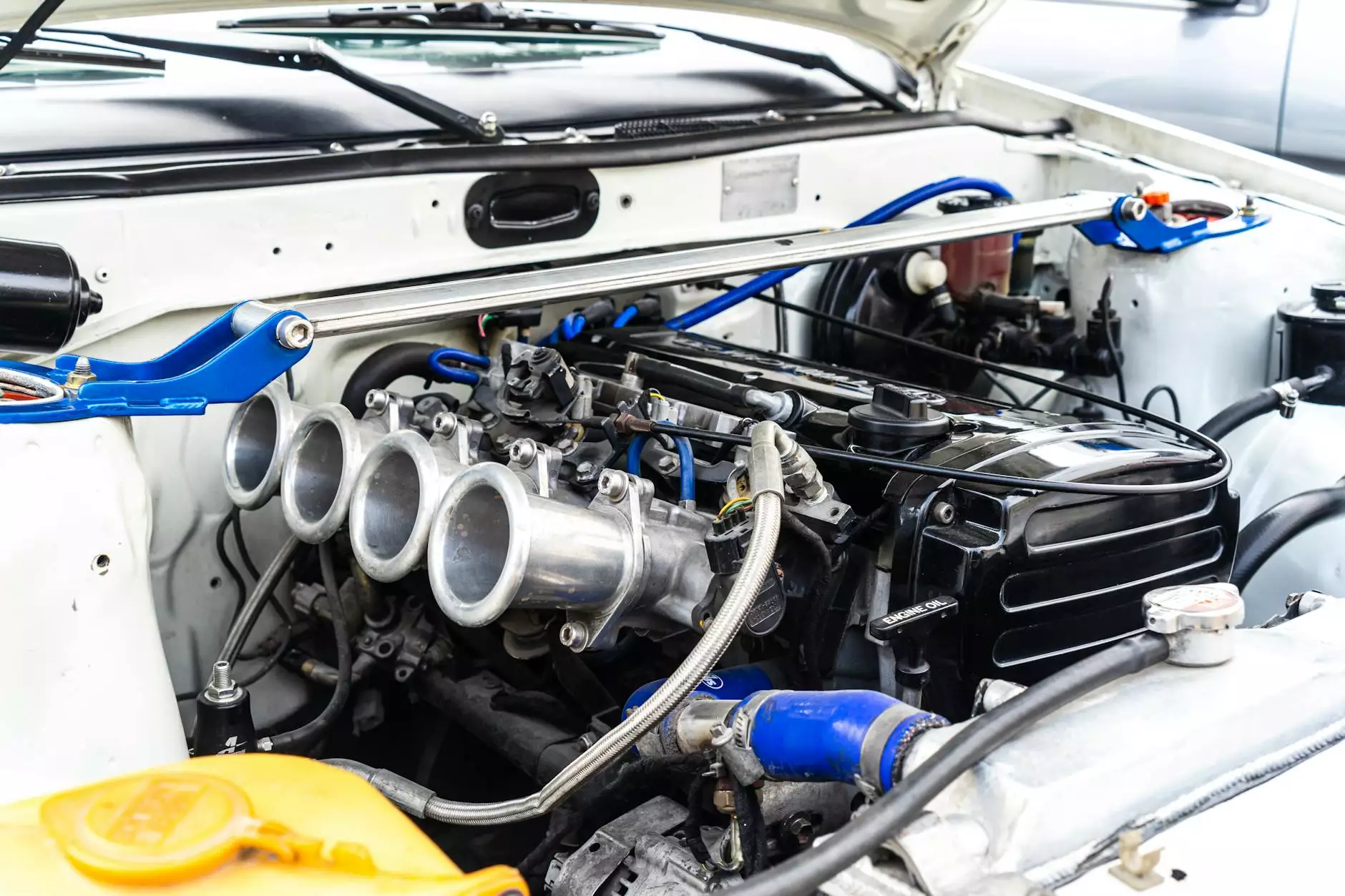
In the world of engineering and fluid dynamics, valves play a crucial role in controlling the flow of fluids. One of the critical components that ensure effective management of fluids in various systems is the manifold valve. This article delves into the manifold valve function, its significance, types, applications, and how it integrates into different industries.
What is a Manifold Valve?
A manifold valve is a comprehensive solution designed to improve the distribution and control of fluids between different parts of a system. Manifold valves serve multiple functions and can handle various tasks depending on their configuration. They are typically used in conjunction with other fittings like tube fittings, ferrule fittings, and check valves, making them an essential component in hydraulic and pneumatic systems.
The Core Function of Manifold Valves
At its essence, the manifold valve function involves controlling the flow, direction, and pressure of fluids within a system. Depending on the design and needs of a particular application, manifold valves can:
- Control Circuitry: Manage fluid flow to specific components, ensuring each part receives the necessary fluid supply.
- Combine Functions: Integrate multiple valve functions into a single housing, reducing piping and space requirements.
- Improve Maintenance: Simplify the maintenance process by grouping several valves together, making it easier to access and service.
- Enhance Safety: Provide control measures to prevent overpressure and other hazardous conditions in fluid systems.
Types of Manifold Valves
Manifold valves come in various forms, each designed to meet specific operational requirements. The following are some common types:
1. Hydraulic Manifold Valves
These valves are specifically designed for hydraulic systems, allowing for the control of hydraulic pressure and fluid flow effectively.
2. Pneumatic Manifold Valves
Pneumatic manifold valves manage compressed air within pneumatic systems, ensuring efficient operation in devices like cylinders and actuators.
3. Instrumentation Manifold Valves
Used in high-precision applications, instrumentation manifold valves manage the flow of fluids and gases in process control and analyzing systems.
4. Solenoid Manifold Valves
These valves incorporate solenoid technology, allowing for automated control of fluid flow, frequently found in electronic applications.
Applications of Manifold Valves
The versatility of the manifold valve function allows it to be implemented across various industries:
- Aerospace: Used in fuel systems, hydraulic control, and landing gear operations.
- Manufacturing: Controls fluid flow in machining and production processes.
- Automotive: Manages hydraulic and pneumatic systems in vehicles.
- Oil and Gas: Integral to the operations of drilling and refining processes.
- Pharmaceuticals: Ensures fluid control in sterilization and mixing processes.
The Importance of Manifold Valves in Engineering
In a complex fluid system, the importance of manifold valves cannot be overstated. Their ability to consolidate multiple functions into a single entity streamlines operations, minimizes errors, and reduces the amount of required piping. This efficiency leads to significant cost savings and lower maintenance requirements. Moreover, manifold valves can also contribute to system safety by providing effective pressure regulation and preventing overpressure scenarios.
Design Considerations for Manifold Valves
When selecting manifold valves, several design considerations should be taken into account:
- Material: Choosing the correct material is essential for compatibility with the fluid type and operating conditions.
- Pressure and Temperature Ratings: Ensure the valve can withstand the pressures and temperatures of the application.
- Flow Capacity: Assess whether the valve can handle the desired flow rates without loss of efficiency.
- Connection Types: Identify the necessary fittings for seamless integration within the system.
Benefits of Utilizing Manifold Valves
Leveraging the manifold valve function offers several advantages:
- Space Saving: The compact design of manifold valves allows for a reduction in the footprint of fluid control systems.
- Cost Efficiency: Their design minimizes the need for additional fittings and piping, leading to overall reduced costs.
- Operational Reliability: Manifold valves are designed for durability, supporting long-term operations in demanding environments.
- Enhanced Performance: By integrating various control functions, manifold valves contribute to improved system efficiency and response times.
Maintenance of Manifold Valves
Regular maintenance is crucial for ensuring the longevity and reliability of manifold valves. This includes:
- Visual Inspections: Regularly check for any visible damage or leaks.
- Cleaning: Keep the valves clean from contaminants that could affect performance.
- Testing: Periodically test the function of the valve through operational checks.
- Professional Servicing: When necessary, arrange for professional maintenance to handle complex issues.
Conclusion: The Vital Role of Manifold Valves
The manifold valve function is a cornerstone of fluid management in numerous industrial applications. Its ability to optimize fluid control through compact and versatile design makes it indispensable in today's engineering landscape. Understanding the intricacies of manifold valves allows businesses, such as Tech Tubes, to harness their potential fully, ensuring efficient and safe operation across various sectors.
As industries continue to evolve, the role of manifold valves will expand, and their functions will become even more integral to technological advancements. By focusing on quality and comprehensive solutions, businesses can improve their operational processes and achieve higher productivity, ultimately benefiting from the robust performance that manifold valves provide.