Understanding Plastic Injection Tools
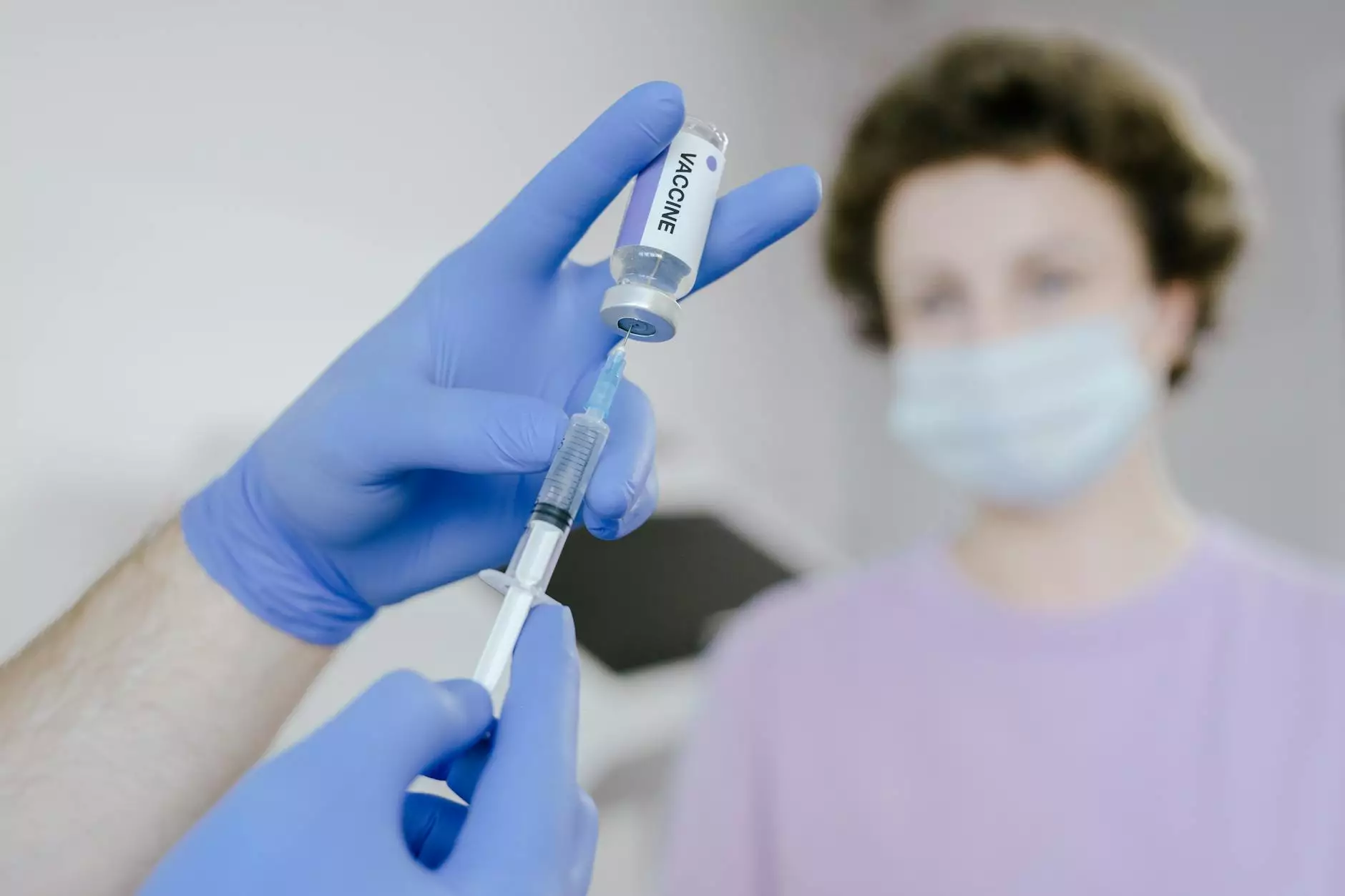
Plastic injection tools are vital in various manufacturing industries, particularly in metal fabrication. These tools enable manufacturers to create intricate designs and components that contribute to the performance and functionality of countless products we use daily. In this comprehensive guide, we will explore the definition, applications, and benefits of plastic injection tools, along with the role they play in modern manufacturing.
What Are Plastic Injection Tools?
Plastic injection tools refer to specialized equipment used in the plastic injection molding process. This process involves melting plastic pellets and injecting the molten material into a mold to create solid plastic parts. These tools are designed to withstand high pressure and temperature, ensuring precision and efficiency in production.
The Components of Plastic Injection Tools
Plastic injection tools consist of several key components:
- Mold: The mold is the most critical part of the injection tool, determining the final shape and size of the product.
- Injection Unit: This component heats and injects the molten plastic into the mold.
- Clamping Unit: The clamping unit securely holds the mold together during the injection process.
- Cooling System: A cooling system is essential to solidify the plastic after injection, allowing for the quick removal of the finished product.
The Process of Plastic Injection Molding
The process of plastic injection molding using these tools can be broken down into several stages:
Stage 1: Material Preparation
Plastic pellets or granules are dried and prepared for melting. This step is crucial to ensure the quality of the finished product, as moisture can lead to defects.
Stage 2: Injection
The prepared material is heated until it transforms into a molten state. The injection unit then injects this molten plastic into the mold under high pressure.
Stage 3: Cooling
After the injection phase, the plastic needs to cool and solidify. The cooling time varies depending on the thickness and complexity of the part.
Stage 4: Ejection
Once the plastic has cooled and solidified, the clamping unit opens, and the finished part is ejected from the mold.
Applications of Plastic Injection Tools in Metal Fabrication
In the realm of metal fabrication, plastic injection tools find various applications, serving as essential components in the production of numerous products. Here are some prominent use cases:
- Automotive Parts: Components like dashboard panels, fittings, and various interior parts are produced using plastic injection molding.
- Consumer Electronics: Many devices use injection-molded plastic components for casings, buttons, and other features.
- Household Appliances: From small appliances to large kitchen devices, plastic injection tools play a vital role in production.
- Medical Devices: Precision components used in medical devices are often manufactured using these tools, ensuring high-quality standards.
Advantages of Using Plastic Injection Tools
The use of plastic injection tools offers several benefits in manufacturing:
1. High Efficiency
Plastic injection molding is known for its speed and efficiency. Once the mold is created, it can produce thousands of identical parts in a short period, significantly reducing production time.
2. Cost-Effectiveness
While the initial investment for injection molds can be significant, the ability to mass-produce parts at a low cost per unit makes this process financially viable for large-scale production.
3. Precision and Consistency
Injection molding provides high precision in part dimensions and shapes, ensuring consistent quality across all products. This is essential in industries like automotive and medical, where exact specifications are crucial.
4. Material Versatility
Plastic injection tools can work with various types of plastic, including thermoplastics and thermosets, allowing manufacturers to choose the best materials for their specific applications.
Challenges in Plastic Injection Molding
While there are many benefits, there are also challenges associated with plastic injection molding:
1. Initial Costs
The initial cost of creating molds can be high, which may deter small businesses from utilizing plastic injection tools.
2. Complex Design Requirements
Designing a mold requires expertise and can be time-consuming, particularly for complex parts.
3. Material Limitations
Not all materials can be injection molded, and certain types of plastics may present challenges in the molding process.
Innovations in Plastic Injection Tools
The field of plastic injection molding is continuously evolving, bringing forth new innovations that enhance efficiency and product quality. Some notable advancements include:
1. 3D Printing Integration
3D printing technology is increasingly being combined with traditional injection molding techniques, allowing for rapid prototyping and design testing before full-scale production.
2. Smart Injection Molding
Manufacturers are now implementing IoT technologies to monitor and control the injection molding process in real-time, ensuring optimal performance and reducing waste.
3. Sustainable Practices
The industry is shifting towards more sustainable practices, including the use of recycled materials and energy-efficient machinery, to reduce environmental impact.
The Future of Plastic Injection Tools in Metal Fabrication
The future of plastic injection tools in metal fabrication is bright, with advancements in technology and materials continuously shaping the industry. As manufacturers strive for greater efficiency and sustainability, plastic injection molding will remain a cornerstone of modern production.
In conclusion, plastic injection tools are indispensable in various sectors, particularly in metal fabrication. Their ability to produce high-quality, precision-engineered products makes them invaluable in today’s manufacturing landscape. As technology progresses and demands evolve, these tools will continue to play a critical role in shaping the future of manufacturing.
Why Choose DeepMould.net for Your Plastic Injection Tool Needs?
DeepMould.net stands out in the industry for its commitment to quality and customer satisfaction. Our expertise in plastic injection tools ensures that our clients receive not only high-quality products but also exceptional service. Here are a few reasons to choose us:
- Expertise: Our team comprises industry experts who possess extensive knowledge of plastic injection tools and their applications.
- Customization: We offer tailored solutions to meet the specific needs of our clients, ensuring maximum efficiency and effectiveness.
- Quality Assurance: Our rigorous quality control processes guarantee that every tool meets the highest standards.
- Innovative Solutions: We stay ahead of industry trends to provide our customers with the latest advancements in plastic injection molding technology.
Final Thoughts
As we have explored throughout this article, plastic injection tools are a vital component in the manufacturing industry, especially within the realm of metal fabrication. Their efficiency, precision, and cost-effectiveness make them indispensable for producing a wide range of products. With ongoing advancements in technology and materials, the role of these tools will only continue to grow. Consider partnering with DeepMould.net for your plastic injection tool needs to leverage our expertise and commitment to excellence.