The Precision of CNC Machines in Metal Fabrication
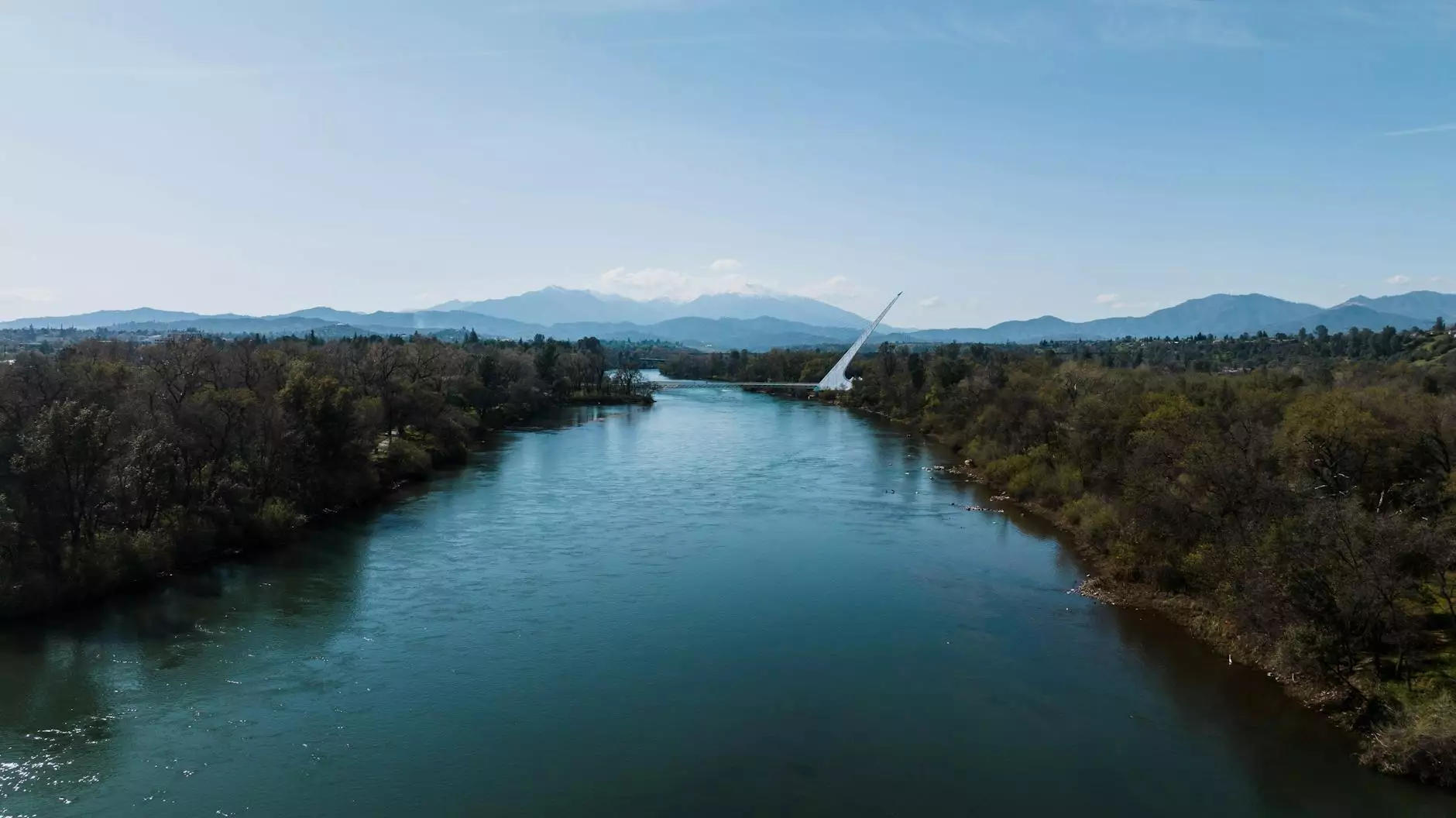
In today's fast-paced manufacturing world, the precision of CNC machines stands out as a game-changer for industries reliant on metal fabrication. These CNC (Computer Numerical Control) machines offer a level of accuracy that conventional machining cannot match, making them indispensable in modern manufacturing.
Understanding CNC Machines
CNC machines operate on a computer-based control system, which directs machinery to fabricate parts based on pre-programmed specifications. This technology is pivotal in ensuring every component produced adheres to strict tolerances and dimensions. The evolution from conventional machining to CNC has empowered businesses to enhance productivity and precision in metal fabrication.
The Components of CNC Machines
CNC machines are composed of several key parts that work in conjunction to achieve high precision:
- Controller: This is the brain of the CNC machine, interpreting the design inputs and generating signals to control the movement of the machinery.
- Drive Motors: These motors move the machinery parts, ensuring accurate positioning and speed control.
- Tooling: The tools used in CNC machines are specifically designed to cut, mill, and shape metal with exceptional accuracy.
- Bed and Framework: A solid foundation that supports the machine and helps absorb vibrations for enhanced precision.
The Role of Precision in Metal Fabrication
The precision of CNC machines directly impacts the quality of metal products. In industries such as aerospace, automotive, and medical device manufacturing, where even the slightest error can result in significant failures, CNC technology eliminates human error and guarantees high-quality outcomes.
Applications of CNC Machines in Metal Fabrication
CNC technology has a wide range of applications in metal fabrication:
- Milling: CNC milling machines are capable of removing material from a workpiece to create complex shapes with high accuracy.
- Turning: CNC lathes are used to produce cylindrical parts with precise dimensions and smooth surface finishes.
- Laser Cutting: CNC laser cutters provide the ability to cut metals at high speeds while maintaining intricate details.
- Plasma Cutting: This technique is essential for cutting thicker metal sheets with non-contact technique.
The Advantages of Using CNC Machines
The transition to CNC technology in metal fabrication presents numerous advantages, such as:
- Increased Efficiency: CNC machines can operate continuously, producing parts faster than manual machining.
- Enhanced Accuracy: The precision of CNC machines ensures parts are manufactured consistently within tight tolerances.
- Customization: CNC technology allows manufacturers to easily adapt to different designs with minimal downtime.
- Reduced Material Waste: Precise cutting techniques lead to less wasted material, resulting in cost savings.
Factors Influencing the Precision of CNC Machines
While the precision of CNC machines is widely known, several factors can affect this accuracy:
- Machine Calibration: Regular calibration is necessary to maintain positioning accuracy and operational efficiency.
- Tool Wear: Dull or damaged tools can adversely affect the quality of the cut and dimensional tolerances.
- Material Properties: The nature of the metal being worked on—such as hardness and thickness—can influence precision.
Innovations in CNC Technology
The world of CNC machining is continually evolving. Innovations in software and hardware are enhancing the precision of CNC machines:
- Advanced Software: CAD/CAM software integration improves design capabilities and machining precision.
- 5-Axis Machining: This technology allows for more complex shapes and geometries to be fabricated with unmatched accuracy.
- Automation: Incorporating robotic arms and automated loading systems increases production rates and reduces human error.
Challenges in CNC Machining
Despite its many advantages, CNC machining does come with challenges:
- High Initial Investment: The acquisition and implementation of CNC machines can require significant capital.
- Training Requirements: Skilled operators are needed to program and maintain CNC systems effectively.
- Software Compatibility: Ensuring that different software systems work well together can be complex.
The Future of CNC Machines in Metal Fabrication
As technology advances, the precision of CNC machines is expected to reach new heights, further blending the boundaries between automation and manual operation. With the advent of Industry 4.0, which integrates smart technologies into manufacturing processes, CNC machines will play an even more critical role in enhancing efficiency, product quality, and operational flexibility.
Conclusion
The precision of CNC machines is not just a technical aspect; it represents the future of metal fabrication. For businesses like Deep Mould, which specializes in metal fabrication, adopting CNC technology is essential for meeting the high standards of quality and efficiency demanded by today’s marketplaces. The benefits of utilizing CNC machines far outweigh the challenges, and as advancements continue, this precision will only enhance the capabilities of manufacturers worldwide, ensuring that they remain competitive and innovative in an ever-evolving industry.
Call to Action
If you are looking to embrace the transformative power of the precision of CNC machines in your metal fabrication processes, contact Deep Mould today. Let us help you enhance your manufacturing capabilities with our state-of-the-art CNC technologies.